Dmg Electronics Pfronten
February 18 - 22, 2014, DMG Mori Seiki opened the doors for visitors to its Deckel Maho factory in Pfronten, Germany. The company anticipated more than 6,000 people would attend the Open House.
DMG MORI will be showcasing its complete range of manufacturing at the traditional DECKEL MAHO Pfronten Open House from Jan. 30 to Feb 3, 2018. Seventy high-tech machines will be on display, including the NTX 3000 as a world premiere and manufacturing processes such as additive manufacturing with a. Untapped productivity potentials lie not only in the technology of the machine tool but also in the environment surrounding actual manufacturing. The technological leadership of DMG machines with regard to controls, motors and electronics is continually advanced at the Competency Centre.
The DMG Mori Seiki Open House in Pfronten, Germany, featured 73 exhibits, including 8 world premiere machines. About 6,000 people attended the event throughout the week.
During the press conference on Tuesday, Dr. Mori, Dr. Kapitza, and Mr. Thönes addressed nearly 100 members of the international media.

As a global corporation continually striving to be the world's largest and most respected international manufacturer of lathes, machining centers, multi-axis turning centers and grinders, we will.
As a designer with a specialty in electronics, you’ll be part of our motivated and highly-qualified team. You’ll be involved in constructional planning, the coordination and oversight of prototypes, special customer-specific projects, and series production. Aug 28, 2017 EMO is the main reference event for DMG MORI and within every edition, the company sets up a huge display of its capabilities. This year more than ever before, AM will play a key role, with the LASERTEC 65 DED (powder-fed) system and the new LASERTEC SLM (powder-bed) system, resulting from the Realizer acquisition. In total over 8 new system launches will provide insights on the. The new DMP 70 from DMG Mori, unveiled at the recent Pfronten open house in January, aims to provide optimum productivity from the smallest footprint. 8 months ago Michael Tyrrell. New generation HMC With experience gained from installing over 6,000 NH and NHX series horizontal machining centres, DMG Mori has introduced a further.
Included among the many exhibits were 19 machines that featured the new DMG MORI design. The NLX2500/700 turning center, the first model of the new X-class series, is designed for cost effectiveness while delivering high accuracy, high rigidity, and high cutting capacity.
A large area of the showroom was dedicated to CELOS technology. Product demonstrations helped visitors see the advantages of multi-touch technology on both the screen and the keypad for navigation and interaction. CELOS is designed to be the basis for a comprehensive shop network that grows in capability as the user downloads application modules similarly to on a mobile device.
The new design of the Lasertec 65 drew a lot of attention. This hybrid solution combines milling and laser metal deposition processes for additive manufacturing. It features a diode laser mounted in place of a cutting tool, and the material is added by spraying metallic powder into the laser beam, melting the powder in layers into the base material.
The world premiere of the DMC 80 FD duoBlock demonstrated heavy machining as well as highly productive series production. The feed drive’s intensive cooling measures provide 30% increased accuracy.
Pfronten and the surrounding area near DMG Mori Seiki’s Deckel Maho factory are beautiful. They complemented well the technology on display inside the facility. This is Neuschwanstein Castle, less than 20 kilometers away.
PreviousNextRead Next
February 18 - 22, 2014, DMG Mori Seiki opened the doors for visitors to its Deckel Maho factory in Pfronten, Germany. The company anticipated more than 6,000 people would attend the Open House throughout the week to view 73 exhibits, including 8 world premieres. Overall, 19 of the machines on display featured the new DMG MORI design, and 18 of those include CELOS.
During Tuesday’s press conference, Dr. Rüdiger Kapitza, chairman of the board for DMG Mori Seiki Aktiengesellschaft, addressed nearly 100 members of the international press, detailing the company’s growth as demonstrated through new technology centers worldwide. Dr. Masahiko Mori, president of DMG Mori Seiki Company Ltd., provided further details about the company’s increased production with the opening of several new factories in the past two years. Christian Thönes, member of the board for DMG Mori Seiki Aktiengesellschaft, discussed the technology on display at the Pfronten Open House. In particular, he detailed the CELOS control technology, which offers a common interface for all of the company’s new machines.
A walk through the showroom and an in-depth tour of the entire Pfronten facility provided insight regarding the extent that the company is addressing the needs of the industry. Including the eight world premieres displayed at this Open House, DMG Mori Seiki will present a total of 24 premieres throughout 2014.
Dmg Electronics Pfronten For Sale
DMG Mori’s 2017 annual press conference in Pfronten, Germany, set the course for the future of the Global One Company in what is expected to be a highly competitive year. Machine tool orders for 2016 reached a record high of € 2,369.9 million, up 4% compared with a global machine tool market that declined 1.7%. Dr. Ing. Masahiko Mori, president DMG Mori Co. Ltd, and Christian Thönes, chairman of the executive board, DMG Mori AG, detailed plans for new organisational sales and service structure, streamlining its operations, and strengthening its additive manufacturing and digitisation capabilities.
Hans-Peter Neth, Executive Chairman of Retecon, chats to Bruce Crawford, publishing editor of Metalworking News, about their recent visit to the DMG MORI Open House event that took place in February 2017 at the Deckel Maho facility in Pfronten, in Southern Germany
In this new world, improving customers’ manufacturing process efficiency requires a wide range of operational resources, establishment of a value chain, including peripherals, development of software to link these systems, design of human-machine interface and collection, analysis and protection of data.
During its annual open house at Deckel Maho in Pfronten, Germany, which is located at the foothills of the Alps and where DMG MORI builds the largest of its machines, the machine tool manufacturing company premiered three new models, displayed a wide range of innovations and said that a new global manufacturing dynamic is beginning to take shape.
Pfronten is one of the leading tourist resorts in southern Bavaria, Germany. In 1920 it was the birthplace of Maho, a manufacturer of milling and boring machines. Today Deckel Maho, a company within DMG MORI, exports milling machines and flexible manufacturing centers from Pfronten to over 100 countries
Annually the DMG MORI Group holds an open house exhibition at the Deckel Maho facility in Pfronten
The 9 000 international trade visitors were greeted by a display area of 8 500m² featuring more than 80 high-tech exhibits and major sector highlights from the fields of automation, digitisation, additive manufacturing and technology excellence.
South African 5-axis machine in assembly
A walk through the showroom and an in-depth tour of the entire Pfronten facility provided insight regarding the extent to which the company is addressing the needs of industry.
Os x 10.7 dmg. Aug 23, 2019 Mac OS X Lion 10.7 ISO/DMG is the eighth major release of Mac OS X is a completely different version from the for windows because it is a version which is totally based on the productivity suite for mac os x.
A highlight for a South African visiting the exhibition was not only being able to see machines in various stages of assembly and being tested, over and above all the machines and services in the exhibition area, but also to pick out a DMU 210P universal milling center that was in the late stages of being assembled. Once completed, the machine is destined to be shipped to a South African client.
The 5-axis CNC machining center allows for easy and efficient machining of parts up to eight tons. This is a large 5-axis machine that uses a stable bridge structure to achieve high accuracy and enables 5-axis machining in a single set. The DMU 210 P is equipped with a NC rotary table and has XYZ working area of 2 100 x 2 100 x 1 250mm.
The XXL Center in Pfronten is dedicated to building 12 large machines per year and represents the company’s systems approach to improving its best sellers. The machine that caught my eye (whose size alone gets your attention) was the DMU 600 Gantry linear, which is quite impressive for mould machining
As has become tradition, the focus of the DMG MORI Open House event at Deckel Maho Pfronten was on the latest innovations and groundbreaking technologies. It is reported that over 9 000 vistors attend the exhibition over five days
Dmg Electronics Pfronten Free
The proven and successful portal series with more than 1000 installed machines is based on a FEM-optimised portal machine design. The thermo-symmetrical construction with liquid-cooled ball screws, feed axes, linear guides and all rotary axes ensures maximum dynamics and long-term accuracy. An optimised extended swivel range and interference contours of the newly developed DMG MORI milling head leading to the optimal usage of the cubic-working space.
In Limitless, the operating principle is that the most transparent limiting is a fixed gain reduction - so we strive for maximal smoothness of the gain reduction signals. With the constraints of peak limiting and maximal smoothness, we designed a numerical solver, which per-sample solves to find the gentlest possible adjustments that will prevent clipping. Dmg limitless orange clipping. Although Limitless is easily the most comprehensively featured limiter I’ve ever come across, DMG have managed to harness all of its power within a friendly and well thought-out user interface. By default, Limitless opens in a fairly small window that presents only the main Threshold, Ceiling and Release time controls on the left, and the output meters on the right. Limitless' Clipper has three algorithm choices: Swell and Swell2 both add third-order harmonic distortion, and the Knee algorithm varies from hard clip (ADC clipping) to soft clip. I tried Swell2 and put the Drive control up to 7.7 dB and set the amount, a mix between the clipped signal and input, to 50 percent. Threshold is the main control used to control Limitless. It sets the threshold at which Limitless should start clipping. Gain is auto-applied to bring this level up to 0dBFS, so dragging down the Threshold increases level in general. 4.2.2 Ceiling Ceiling is an output gain after all the limiting has taken place. It sets the output level for the plugin.
DMG MORI’s history in Pfronten
Pfronten is one of the leading tourist resorts in southern Bavaria, Germany. In 1920 it was the birthplace of Maho, a manufacturer of milling and boring machines, when five engineers founded Maho AG as Mayr, Hoermann & Cie GmbH. In 1993 Friedrich Deckel AG and Maho AG merged into Deckel Maho. The firm of Friedrich Deckel, established in 1903, did not begin as a machine tool company but as a camera shutter manufacturer (associated primarily with the famous “Compur” shutter). They ended up manufacturing their own machinery for this, and at some point began offering this machinery for sale.
In 1994 Gildmeister AG acquired Deckel Maho AG and was renamed Deckel Maho Gildmeister AG. Friedrich Gildemeister had founded Gildemeister & Company in Bielefeld, Germany in 1870. In 1906 the company started mass production of machine tools and in 1910 management decided to concentrate on its flagship products: turret lathes, multi-spindle automatic lathes, milling machines and vertical and horizontal milling machines.
Visitors were allowed to walk through the whole plant in Pfronten. Here we see automatic tool changer carousels being tested
A highlight for a South African visiting the exhibition was not only being able to see machines in various stages of assembly and being tested, over and above all the machines and services in the exhibition area, but also to pick out a DMU 210P universal milling center that was in the late stages of being assembled. Once completed, the machine is destined to be shipped to a South African client
In 1950 the first Maho milling machine was introduced, the predecessor to all Maho universal milling machines. Originally, the company produced compasses and precision drawing instruments. By 1960, milling machines accounted for three-quarters of the company’s sales. Since 1985, Maho has concentrated on producing milling machines with contouring control and on machining centers.
In the plant in Pfronten, over 950 people are employed in machine development and production, and in the sales, training and service departments. Deckel Maho trains over 200 apprentice machinists, toolmakers, electricians, electronics specialists and draftspersons. These people are employed by Deckel Maho itself, and by the numerous small companies in the area, many of which are suppliers to Deckel Maho.
Deckel Maho milling machines and flexible manufacturing centers are exported from Pfronten to over 100 countries.
DMG MORI’s recent history dates back to 2009 when Japanese machine tool builder Mori Seiki and Deckel Maho Gildmeister AG (DMG) entered into a business collaboration, before acquiring a 5% shareholding in DMG. The two companies changed the name to DMG Mori Seiki and eventually last year to DMG MORI. During this period a number of share purchases took place between the two companies before in April 2016 DMG Mori Co of Japan acquired additional shares in DMG MORI AG to take it up to 76.03% ownership.
DMG MORI acquires majority share in additive manufacturing firm Realizer
DMG MORI is strengthening its position in the additive manufacturing industry with a 50.1% acquisition of the shares in German AM leader, Realizer.
As a global manufacturer of CNC-controlled lathes and milling machines, DMG MORI plans to significantly expand its capabilities with the integration of Realizer’s selective laser melting (SLM) technology.
Realizer has more than 20 years of experience in the industry developing its SLM systems that will now continue to be assembled at both Realizer’s location in Borchen, Germany and at the DMG MORI site in Bielefeld, Germany
“DMG MORI is focusing on strengthening its future technologies,” said Christian Thönes, Chairman of the Executive Board of DMG MORI AG at the press conference held during the exhibition.
“With selective laser melting DMG MORI is bundling the most important generative production processes for metallic materials under one roof. DMG MORI already has extensive know-how in the field of laser deposit welding with powder nozzles through Sauer GmbH.”
Peter Visser of South Africa with Franz Studer of Retecon Machine Tools
Rudi Britz of South Africa with Hans-Peter Neth, the CEO of Retecon Machine Tools
DMG MORI has already shown an active interest in the impact of additive manufacturing on the industry with the introduction of its Lasertec 65 3D system, a hybrid AM and 5-axis milling machine that combines the flexibility of AM with the precision of metal cutting.
The two leading production technologies enable complex, metallic components to be produced from powder. For this purpose a wide variety of weldable materials up to and including multi-material applications can be made use of.
The Realizer deal shows that the company is looking to accelerate this further as the demand from manufacturers for both traditional and AM solutions continues to grow.
World premiere: Lasertec 75 Shape
With its Lasertec 75 Shape DMG MORI expands its portfolio in laser texturing of defined, technical surface structures by means of layer-by-layer material removal using a 3D laser. The machine is equipped with a 100W fiber laser and CELOS® for simplest operation and full integration in the company organisation.
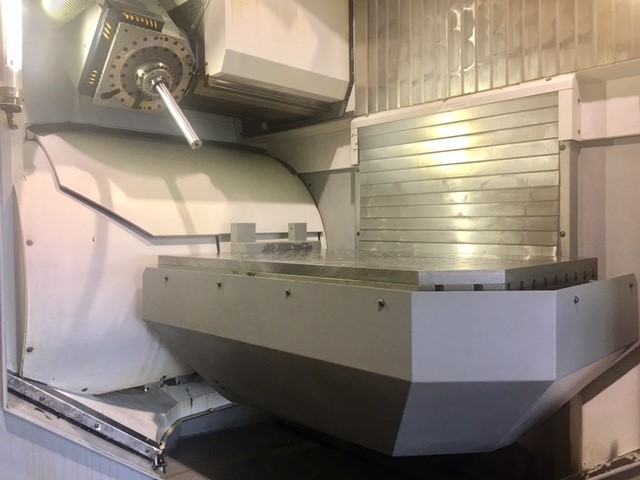
With a footprint of just 8m² the Lasertec 75 Shape is ideally suited for the tightest of production environments but nevertheless offers a work area that can handle workpieces with diameters of 650mm and heights of 500mm. The NC swivel-rotary table is designed for components weighing up to 600kg. The Lasertec 75 Shape masters fast texturing, even in 3D free-form, with no problem at all thanks to contour-parallel laser shaping, which in turn does away with the need for any expensive, environmentally harmful etching. The modern control philosophy based on the Siemens 840 D solutionline plus user-friendly Lasersoft software features round off the offer of the new model.
Lasertec 30 SLM
DMG MORI presented powder bed technology with the Lasertec 30 SLM at the Pfronten exhibition. The Lasertec 30 SLM build volume is 300 by 300 by 300mm, and offers laser sources (IPG) whose power ranges from 400W to 1kW. Layer thicknesses range from 20 to 100micron. More importantly, all reactive materials can be used on the Lasertec 30 SLM as manufacturing takes place in an argon chamber.
The path of digitisation. DMG MORI has established ISTOS, a company that is developing digital production projects
DMG MORI is strengthening its position in the additive manufacturing industry with a 50.1% acquisition of the shares in German AM leader, Realizer. At the exhibition DMG MORI showed off this tie up with the launch of a powder bed technology machine – the Lasertec 30 SLM
“This is the perfect complement to our high-tech machines in the field of Advanced Technologies. Selective laser melting in the powder bed opens up completely new areas of application for our customers,” said Thönes.
Other world premieres – CLX 350 turning center
As the latest model in this segment, the CLX 350 universal turning center expands the portfolio of high-performance basic machines from DMG MORI. In its standard version this compact model, with a footprint of less than 5m², machines bar material of Ø51mm, with Ø65mm also available as an option. The maximum turning diameter of the CLX 350 is 320mm. It has travel paths of 242.5mm in the X-axis and 530mm in the Z-axis. The VDI 30 servo turret has space for twelve tools – powered as an option. This all adds up to make the CLX 350 an efficient and highly productive universal turning machine for a multitude of different applications.
With a speed of 5 000 rpm the highly dynamic spindle can machine complex, high-quality components and guarantees maximum precision and accuracy of the workpiece. The labyrinth structure and air-cooling prevent the penetration of coolant thus promising a high level of productivity and a long life cycle. The replacement cartridge means the spindle can be changed quickly and simply, even during servicing. The ball screw, with a tolerance class of IT 1, also plays a key role where precision and outstanding surface quality are concerned. The compact and stable design of the machine ensures maximum rigidity, even in the boundary areas of machining, as well as optimum chip removal. Thanks to its 19” multi-touch control from Siemens, the CLX 350 also offers the user fast and simple operation combined with perfect ergonomics and compact dimensions.
3rd Generation DMU 50
The new DMU 50 3rd Generation from DMG MORI combines more than 20 years of experience in 5-axis milling with unique future technologies and sets new standards in 5-sided to simultaneous 5-axis machining. With its enlarged swivel range, more powerful spindle and its innovative cooling concept, the world premiere ensures competitive ability in many areas of application for demanding branches such as the aerospace, medical and automotive industries.
With its Lasertec 75 Shape DMG MORI expands its portfolio in laser texturing of defined, technical surface structures by means of layer-by-layer material removal using a 3D laser
The new DMU 50 3rd Generation from DMG MORI combines more than 20 years of experience in 5-axis milling with unique future technologies and sets new standards in 5-sided to simultaneous 5-axis machining
A travel path of 650 x 520 x 475mm and workpiece weights of up to 300kg mean the new 3rd Generation DMU 50 covers a wide range of components. Its new NC swivel-rotary table with an enlarged swivel range of -35°/+110° boosts this versatility. A rapid traverse of 42m/min and 30 rpm in the swivel-rotary axis ensure the dynamics for 5-sided to simultaneous 5-axis machining. The user has the choice of motor spindles with speeds up to 20 000 rpm in addition to the 12 000 rpm inline spindle. Also available as an option is an expanded tool magazine with up to 120 pockets. There are 30 tool pockets in the standard version. The 3rd Generation DMU 50 achieves a degree of precision that is unbeatable in this segment thanks to its one-piece machine bed on the one hand and on the other its innovative cooling of the guides and drives.
DMG MORI establishes ISTOS company for digital production
With the founding of the start-up ISTOS, DMG MORI is expanding its digitisation expertise. The new Düsseldorf-based company is developing digital production projects for DMG MORI and interested partners. The aim is to support DMG MORI’s customers and companies outside the machine tool industry in handling the digital transformation by way of fully connected production processes. For DMG MORI customers ISTOS is the connecting link from an open network across all machines to an integrated digital factory.
ISTOS stands for “Innovative Software Technologies for Open Solutions” and will sustainably shape digitisation in the field of machining. The basis is provided by Celos, the APP based control and operations software from DMG MORI.
“With ISTOS we have successfully managed to attract and gain a complete team of 15 experienced IoT experts. By establishing ISTOS we are speeding up our digital innovation process. I am convinced that ISTOS will support us and our customers with innovative solutions for digitisation,” said Thönes.
With a current share of 85%, DMG MORI is purposefully creating an open structure for further partners or strategic investment and is therefore creating room for digital alliances – even across sectors. ISTOS will develop individual customer solutions across the group and together with DMG MORI Software Solutions GmbH will realise the digital production world. Initial results will be presented at the EMO in Hannover, Germany (18-23 September 2017).
Not just about the machines
As has become tradition, the focus of the DMG MORI Open House event at Deckel Maho Pfronten was on the latest innovations and groundbreaking technologies. Machines were presented according to areas of industry such as aerospace, automotive, die and mold, gear production, general machining, heavy industry and medical and dental, digital factory and additive manufacturing.
Industry 4.0 was also prominent
For DMG MORI, Industry 4.0 in process and product, means supporting customers with software in every process step. At the exhibition DMG MORI presented CELOS® Factory, the complete process chain, from the idea to the finished product. Highlights of Powertools for automatic CAM programming, CELOS®, and Industry 4.0 were presented demonstrating the production of a component right through to the intelligent machine. Additionally, new automation solutions, like Robo2Go, were showcased and a flexible production system unveiled.
The trend towards the networking of machines, products and services to form digital process chains is unbroken. To the same degree, sensors and software are gaining in importance – even in the machine-tool industry.
For this reason, DMG MORI is continuing to massively expand its software solutions. The overriding objective is to generate added value for customers right in the early stages of their digitalisation by means of specific digital solutions. Among other things, this is demonstrated in 26 exclusive DMG MORI technology cycles (Apps) for quick and easy shop floor programming.
Other world premieres included the launch of the CLX 350 turning center
The new DMG MORI Powertools for the automatic creation of programmes in production engineering are a second example. In parallel with this, DMG MORI is vehemently reinforcing its app-based control and operating system CELOS® with the continuous addition of new, targeted applications and solution packages.
Technology Library enables hole sequences and tool technologies to be saved and retrieved at the press of a button.
The new “Adaptive Process” CAM module allows you to keep control of quality. In conjunction with measuring probes and CNC, this enables components to be automatically aligned in the process from the programme in order to machine without errors and to record the results.
The CAM Agent is the new CAM module from DMG MORI for the Based Manufacturing feature. Once component families have been learned in the CAD software, the appropriate NC programmes are then automatically created while maintaining all previously defined sequences and technologies. Programmes are automatically matched to existing tools and technologies even when changing machines.
The Virtual Machine ensures trouble-free machining and minimum setup times in practice. DMG MORI’s unique 1:1 simulation has now been further improved with numerous new functions. Among other things, the simple transfer to the simulation software of clamping devices, zero points and table positions as well as tools and NC programmes have been improved thanks to new DMG-MORI-specific interfaces. This now enables both efficient multi-machine operation and unmanned production to be carried out with maximum process safety.
In addition, a core element of DMG MORI‘s future product strategy is pre-configured CELOS® app solutions. At an attractive, all-inclusive price, they fulfil clearly defined core tasks in digitisation, and thus make the introduction to digitalisation easier for the customer. An example of this is the new CELOS® Performance Package for determining and visualising machine states and parameters. This includes the CELOS® Condition Analyser for analysing machines and process signals, and the CELOS® Performance Monitor for maximum transparency and monitoring of manufacturing parameters.
On the automation side the LPP 24 system provides a total of 24 pallet spaces on two levels. Optionally, due to the modular LPP system, even 99 spaces are possible. Its core elements are the horizontal machining centers NHX 5000 and DMC 60 H linear.
Adding grinding technology to milling and turning in a single set-up
The duoBLOCK® FDS (F-mill D-turn S-grind) series allows milling, turning and grinding to be carried out in a single set-up, so deviations resulting from retooling are also eliminated.
DMG MORI supports the grinding process of the FDS models in the duoBLOCK® series with DMG MORI technology cycles for internal, external and face grinding. Truing cycles expand the range of functions. Also new is an AE sensor (Acoustic, Emission) that guarantees maximum reliability and accuracy by detecting the first contact between the grinding wheel and the truing unit. The first contact between the grinding wheel and the component is also determined via the spindle load factor. DMG MORI has equipped the 1 300 litre coolant unit of the FDS machines with a centrifugal filter that catches even the finest particles (> 10 µm) from the grinding process.
DMU 600 Gantry linear
One standout for me was the XXL Center that is dedicated to building 12 large machines per year and represents the company’s systems approach to improving its best sellers. The machine that caught my eye (whose size alone gets your attention) was the DMU 600 Gantry linear, which is quite impressive for mould machining. This universal, high-speed cutting machine is for five-side/five-axis machining of large workpieces and is said to set new standards in dynamics and surface quality.
The gantry machine is designed as standard for a component weight of 150 000kg, at a point load of 15 000 kg/m². The table measures 5 000 x 3 000mm in a work area of 6 000 x 3 500 x 1 500mm in the standard configuration. The plunger with optimised interference contour enables travel of optionally up to 2 000mm in the Z-direction, the Y-axis crossbeam of 4 500mm and the X-axis can be lengthened as desired.
For more information contact Retecon Machine Tools on TEL: 011 976 8600 or visit www.retecon.co.za